Electromechanical bogie test rig for high precision testing
Optimize bogie performance with precise measurements and minimal maintenance, enhancing safety and reducing operational costs in high-speed train applications.
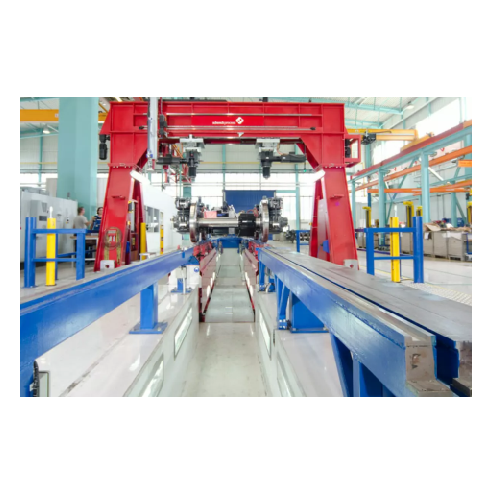
The MULTIRAIL BogieLoad Pro from Schenck Process is an advanced electromechanical bogie test rig, designed for precision and efficiency in rail vehicle development and maintenance. Its fully electromechanical operation utilizes spindle technology for precise positioning and measurement of bogies, making it ideal for applications such as air and secondary suspension testing. This system integrates seamlessly into rail manufacturing lines, providing high-speed, fully automated testing to ensure maximum safety and durability in high-speed trains. Capable of handling a variety of bogie sizes and configurations, the BogieLoad Pro minimizes setup times and maintenance costs, while enhancing test accuracy. It is a comprehensive solution tailored for R&D teams and maintenance providers striving to maintain rigorous safety standards and operational efficiency.
Benefits
- Enhances safety and reliability by ensuring precise bogie testing for rail systems.
- Reduces maintenance costs with fully automatic operation and minimal setup times.
- Optimizes production efficiency by accommodating a wide range of bogie sizes and types.
- Minimizes wear and operational disruptions with robust electromechanical design.
- Supports regulatory compliance and safety standards in rail vehicle manufacturing.
- Applications
- Rail systems,High-speed trains,Air suspension testing,Bogie testing,Vehicle development,Secondary suspension testing
- End products
- Rail vehicle bogies,Air suspension systems for trains,Secondary suspension systems for rail vehicles,High-speed train bogies
- Steps before
- Vehicle Development,Bogie Maintenance,New Bogie Construction
- Steps after
- Safety Assurance,Wear Minimization,Maintenance and Servicing
- Input ingredients
- Output ingredients
- Market info
- Schenck Process is known for its expertise in material handling, weighing, feeding, and automation solutions. The company has a strong reputation for delivering high-quality engineered-to-order equipment for diverse industries, backed by innovative technology and customer-centric service.
- Design Type
- Fully electromechanical with spindle technology
- Positioning Accuracy
- Fully automatic positioning of the bogie
- Max Product Variety
- High variety support
- Testing Flexibility
- Ultra-flexible testing facilities
- Setup Time
- Minimal
- Test Facility Application
- Bogie testing for high-speed trains and vehicle development
- Safety Enhancement
- Improved safety,less wear
- Maintenance and Servicing Cost
- Minimal
- Bogie Types and Sizes
- Wide range
- Working mechanism
- Fully electromechanical design
- Efficiency
- High efficiency with spindle technology
- Automation level
- Fully automatic positioning
- Flexibility
- Ultra-flexible testing facilities
- Precision
- High level of precision
- Setup time
- Minimal setup times
- Product variety handling
- Maximum product variety
- Maintenance
- Less wear and minimum maintenance
- Density/particle size
- 0.5–2.5 g/cm³ / 50–1000 µm
- Footprint
- Compact/Efficient
- Design type
- Fully electromechanical
- Positioning method
- Fully automatic
- Spindle technology
- Present
- Capacity
- Various bogie types and sizes
- Installation
- Indoor,workshop compatibility
- Material
- High-precision components
- Maintenance
- Minimal required
- Control system
- Fully automatic
- Design type
- Fully electromechanical with spindle technology
- Positioning system
- Automatic positioning of bogie
- Testing flexibility
- Ultra-flexible
- Setup time
- Minimal
- Bogie compatibility
- Wide range of types and sizes
- Integration possibilities
- High-speed train testing,vehicle development,special tests