
Lithium-Ion Battery Manufacturing Equipment
Find innovative production technology for making lithium-ion batteries and connect directly with world-leading specialists
Landline telephones in the 1980s were minimalist gadgets that kept getting slimmer in the 1990s. In contrast, cell phones in the same period were bulky and cumbersome. And once they lost their charge, they turned into a giant paperweight. Then came a revolution in batteries and automation with lithium-ion battery manufacturing equipment. Mobile phones packed more power, recharged faster, and endured more recharge cycles. Above all, they were light and small, making cell phones the inseparable companions they are today. But Lithium-ion batteries power much more than phones. As a result, the world is seeing steady growth in battery manufacturing equipment and lithium-ion production lines.
Tell us about your production challenge
Dry and refine lithium before processing the metal
The crucial element in lithium-ion battery production is, of course, lithium. The lightest material on earth is highly reactive, making it a prime candidate for this exchange of electrons.
The metal is obtained either from ore mines or extracted from lithium-rich pools. The former method is quarried and refined; in the latter, the water is removed by evaporators, and the metal is filtered from the remaining deposits.
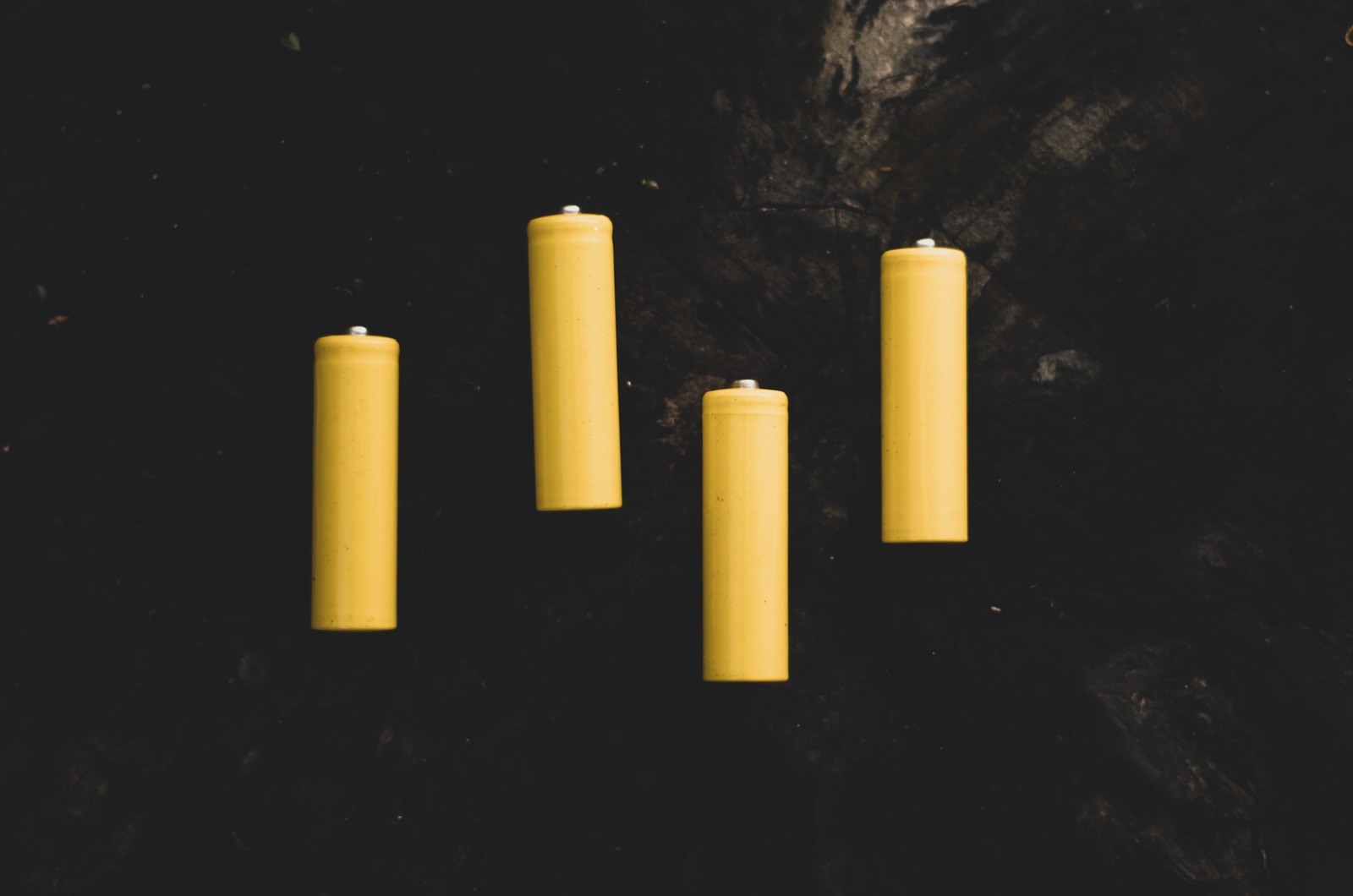
Stabilize lithium with a metal oxide
Lithium is a chemically unstable material, and it is worked into matrices with other metals to stabilize it. Engineers use multiple compounds to form these metal oxides for the cathode chamber. Nickel, manganese, cobalt, aluminum, and iron are the most widely used metals in the cell manufacturing process.
The anode chamber is typically made from graphite, a stable mineral that can hold the lithium ions discharged from the metal oxide.
Enlarge the surface area of lithium particles with fine milling technology
Before starting the formulation process, the raw metals need to be treated with a dryer to remove all moisture content.
Your dry materials are now ready for ultra-fine milling. Grind the metals into a powder to achieve a uniform particle size distribution that allows them to be worked more smoothly. Meanwhile, reducing particle size increases their surface area and produces a higher performance in batteries.
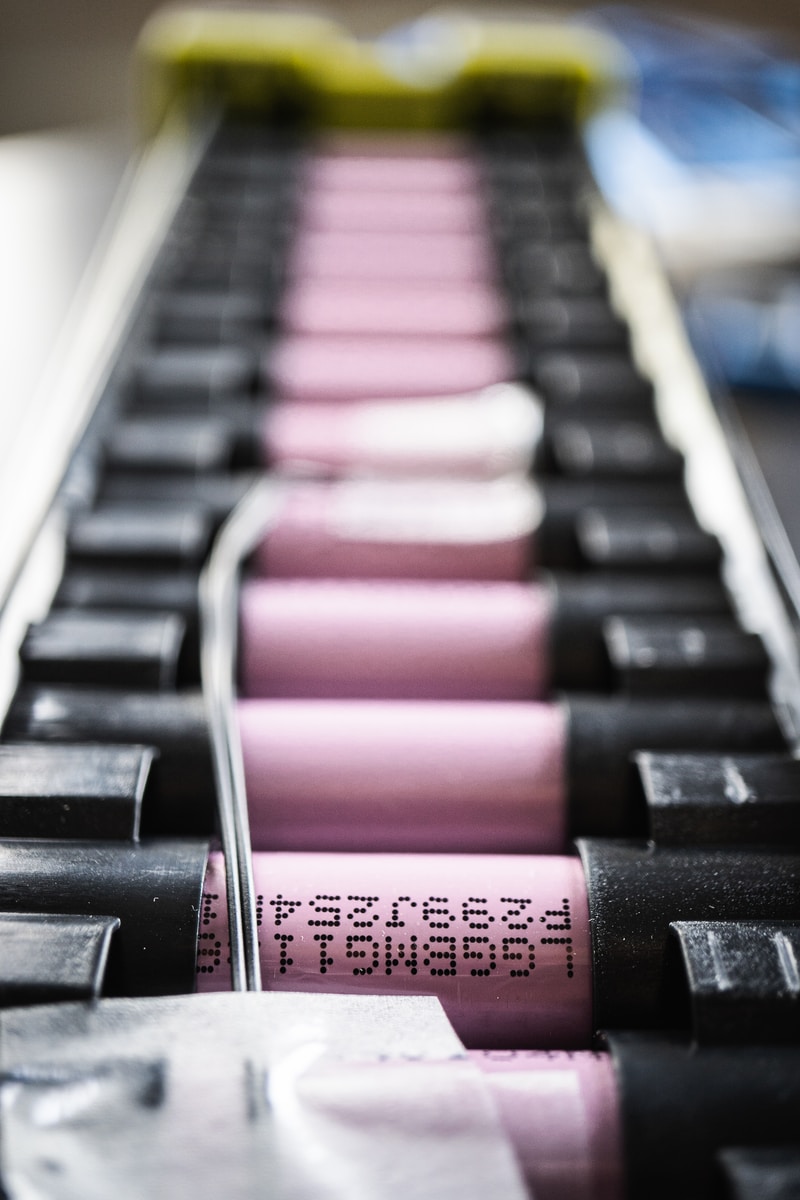
Form the lithium-ion mechanism into a battery cell
The graphite and metal oxides are coded onto current collector sheets, usually made of copper and aluminum on an assembly line. An electrolyte sheet sandwiched between them keeps them from coming into contact. It also serves as a barrier to electrons traveling from cathode to anode and back. Welding techniques, such as laser welding, are used to seal the battery cells, ensuring that they are safe and durable.
The pouch cell design is becoming increasingly popular, as it is lightweight and flexible, making it ideal for portable devices. Cell assembly is the process of assembling the different components of the battery cell, including the anode, cathode, and electrolyte.
The sheets are pressed together and wound around a steel cylinder, forming a compact cell. A typical battery pack module for electric vehicles consists of several lithium-ion battery cells packed together in an integrated unit. The whole is greater than the sum of its parts, and this solution generates electricity more efficiently than a large battery would.
Lithium-ion technology is changing electricity distribution methods
Advances in lithium-ion battery materials and technologies are fast-tracking electric mobility and promise to remodel electricity grids. The basic principle of the battery is that ions and electrons travel from a positive electrode (anode) to a negative electrode (cathode), creating an electric current on the way.
When the anode discharges all its ions, the current is interrupted, and the battery goes flat as the energy storage has been depleted. When you plug your battery-operated device into the wall socket, the positive charge pulls the ions to the anode again. With the development of advanced coater technology, battery manufacturers can now achieve a more efficient assembly line, with the ability to coat multiple layers of materials onto the current collector sheets in a single pass. This not only increases production speed but also improves product quality and consistency.
Which lithium-ion batteries technology do you need?
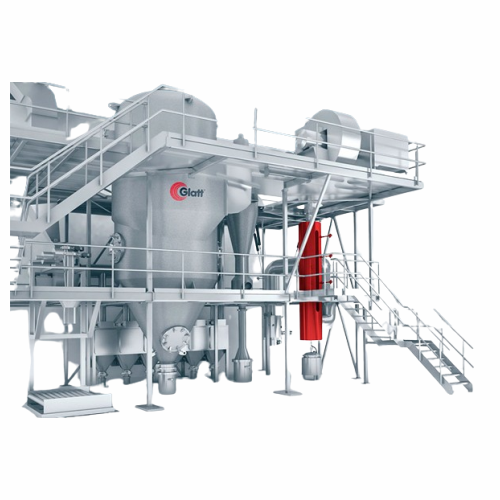
Powder synthesis reactors for nanometer and micrometer particles
Industrial production of high-quality powder materials ...
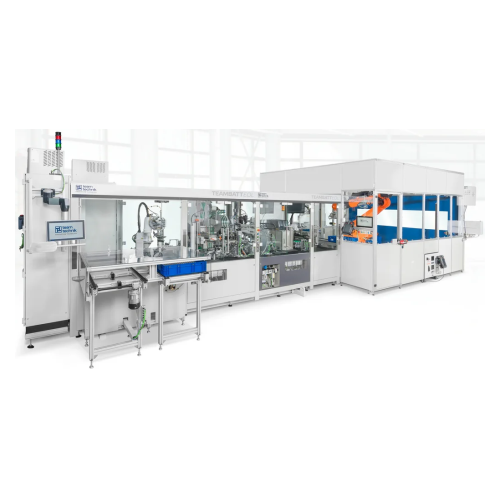
Production systems for battery cells with end-of-line testing
In the manufacturing of battery cells, ensuring quality co...

Battery electrode coating line
In the production of lithium-ion batteries, precise and efficient electrode coating is critic...
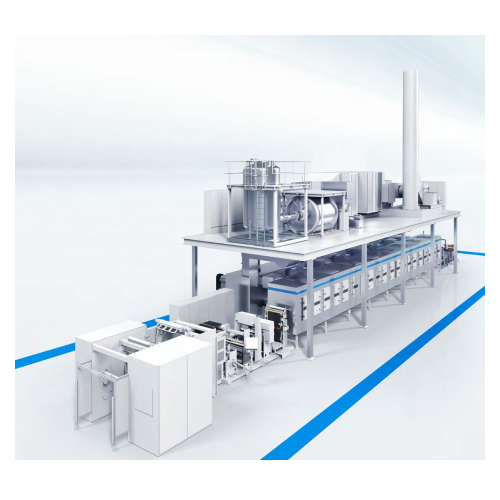
Electrode coating system for lithium-ion batteries
In the production of lithium-ion batteries, achieving consistent and p...
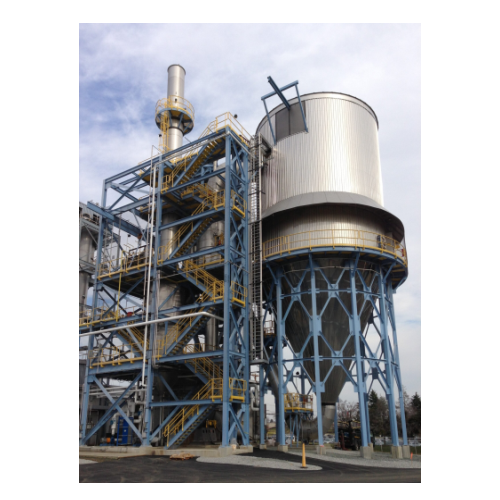
Spray dryers for lithium iron phosphate powder production
In the automotive industry, transitioning to electric vehicles...
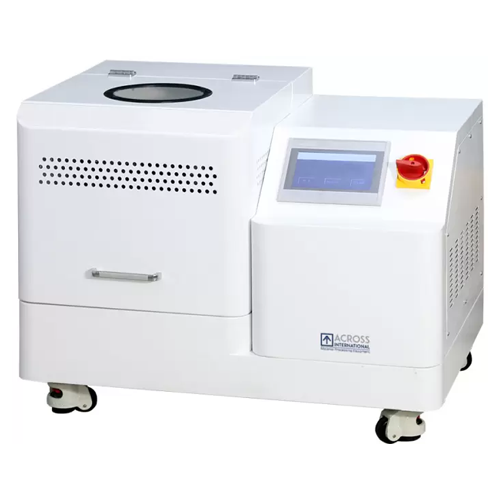
Planetary ball mill for powder material mixing and alloying
In research and industrial applications, precise mixing and ...
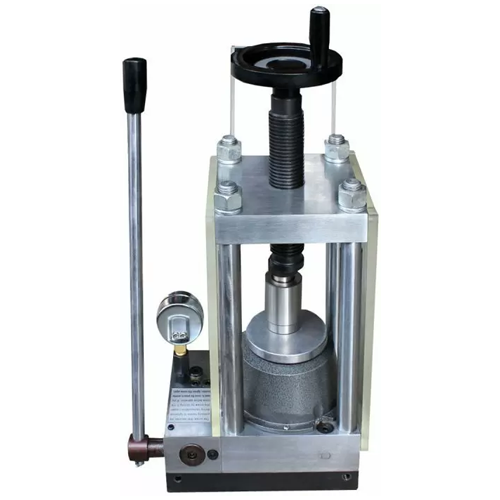
24-ton laboratory pellet press
Preparing compound samples with consistent density and quality can be challenging in material...
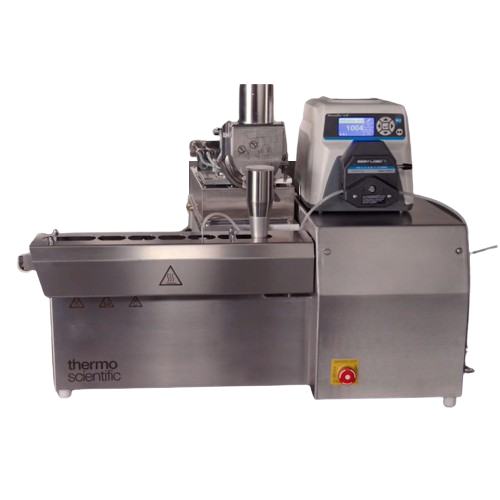
Glovebox for lithium-ion battery material processing
Processing lithium-ion battery materials necessitates a controlled e...
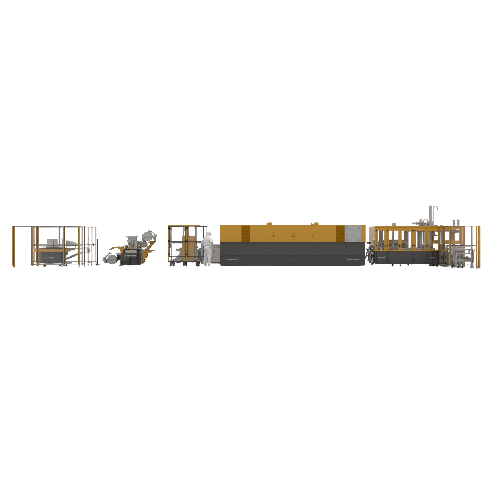
Pasting line for e-bike plates
In the production of e-bike batteries, the need for consistent, high-quality plate pasting is...
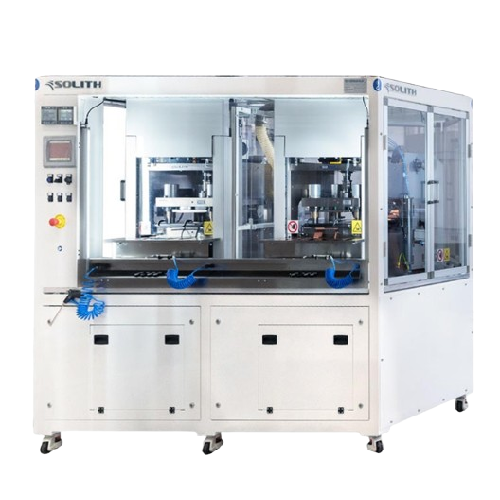
Pouch li-ion cell assembly line
In the battery manufacturing sector, producing high-quality and reliable Li-Ion cells effici...

Roll to roll notching equipment for battery production
In battery manufacturing, precise and clean notching of electrode ...
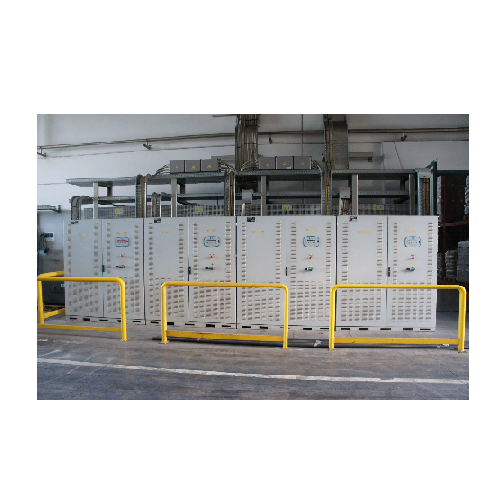
End of line testing for industrial batteries
Ensuring the reliability and safety of industrial batteries is critical durin...
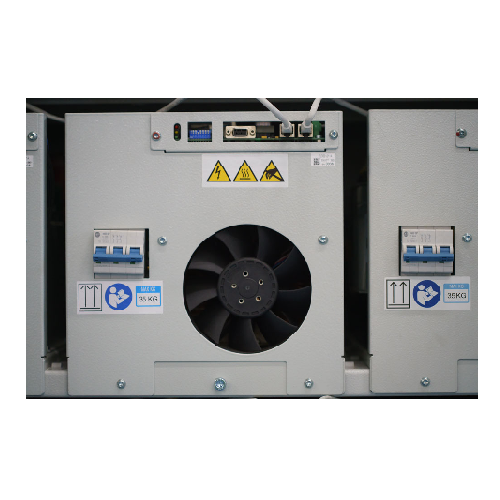
High-density battery chargers
In industrial facilities, ensuring that batteries for heavy-duty equipment are charged efficie...
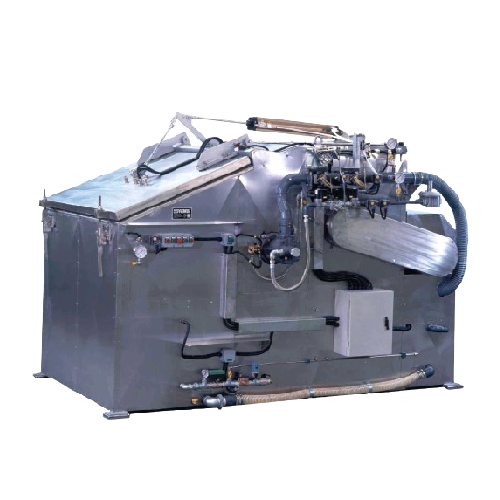
Eft chargers for industrial applications
In environments where battery-operated systems are critical, ensuring efficient an...
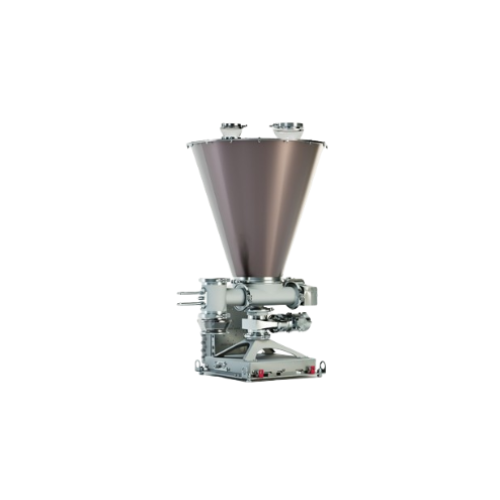
Loss-in-weight feeder for battery cell production
In battery cell production, handling materials safely while maintaining...
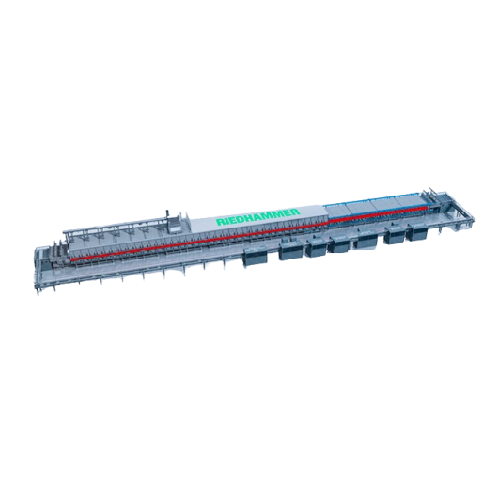
Lithium-ion battery powder processing solution
In industries focusing on next-generation lithium-ion batteries, the proces...
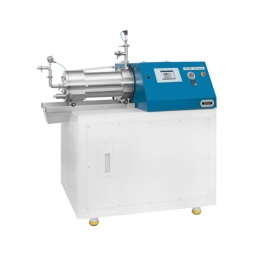
Ultrafine bead mill for battery materials
To facilitate the attainment of ultrafine particles and enhance electrode proper...
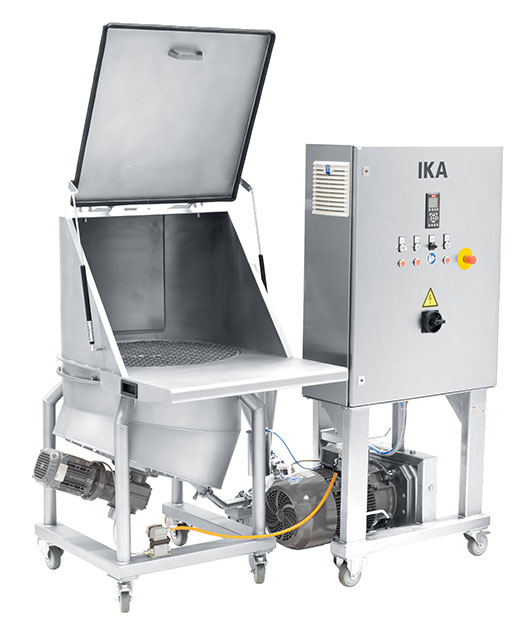
Inline solid-liquid mixer for battery production
In battery production, a critical phase entails mixing solids with liquid...
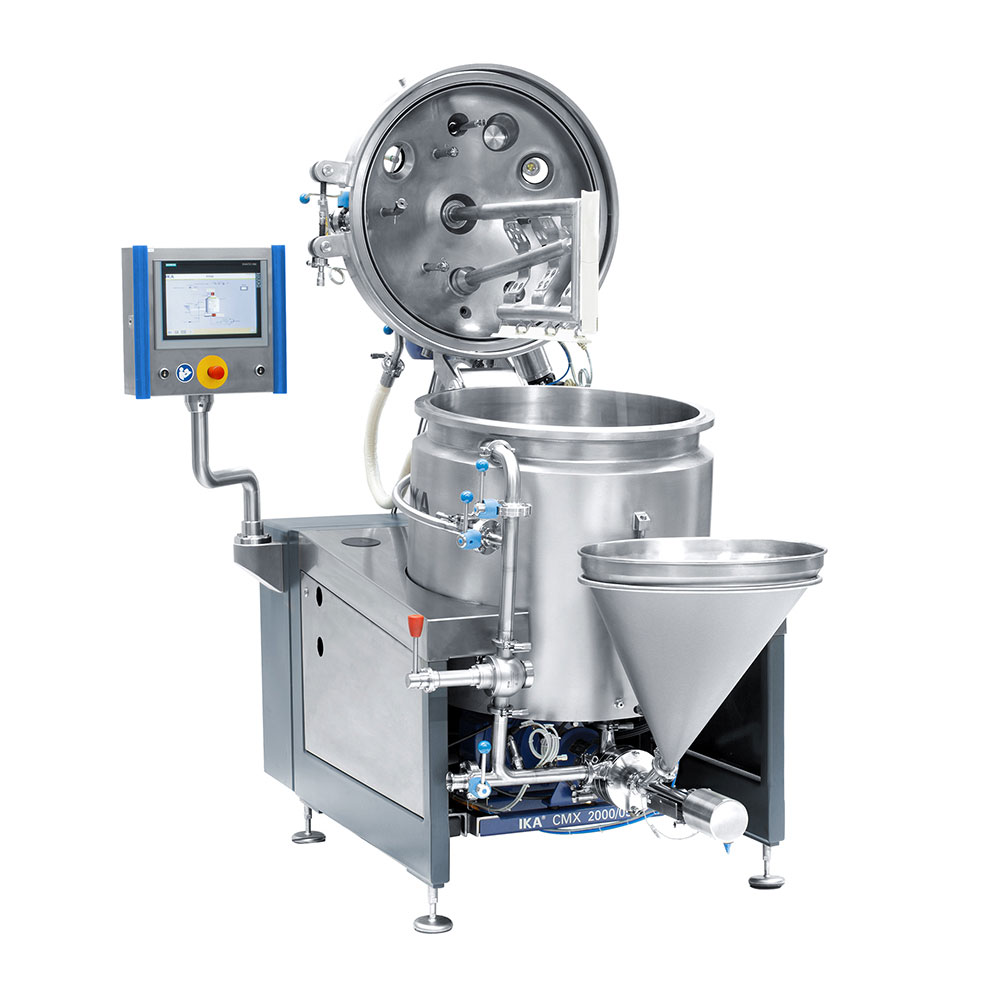
Compact Mixing Plant for Paints and Coatings
A smooth finish in paints and coatings depends on the grade of dispersal duri...

Single-use containment valves
From GMP and HSE perspective material transfer is critical for chemical and pharmaceutical for...
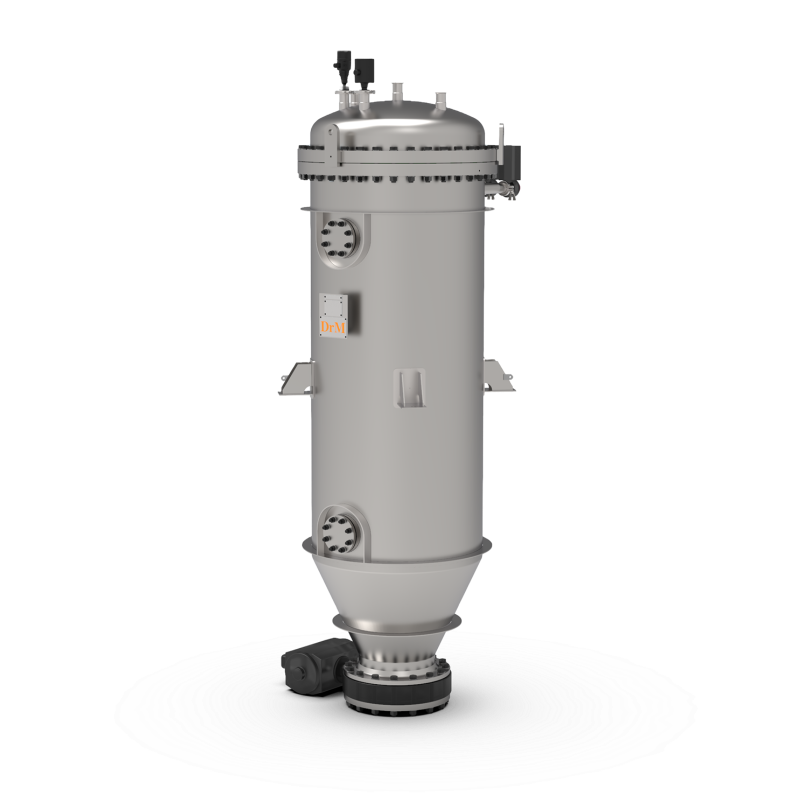
Self-cleaning candle filtration system
Separating solids from liquids by filtration requires frequent cleaning or replaceme...

Automatic centrifuge for lithium carbonate
The battery industry requires high purity components. To obtain more than 99.5%...
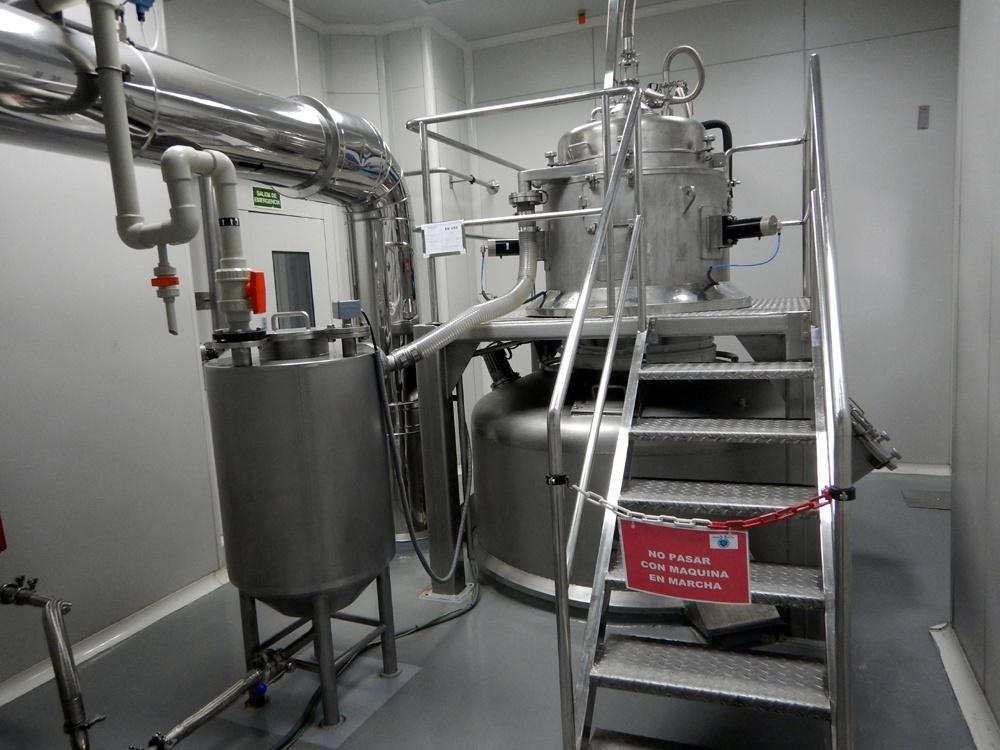
Continuous centrifuge for lithium hydroxide
Lithium hydroxide, a lithium compound used in making lithium batteries, is ind...
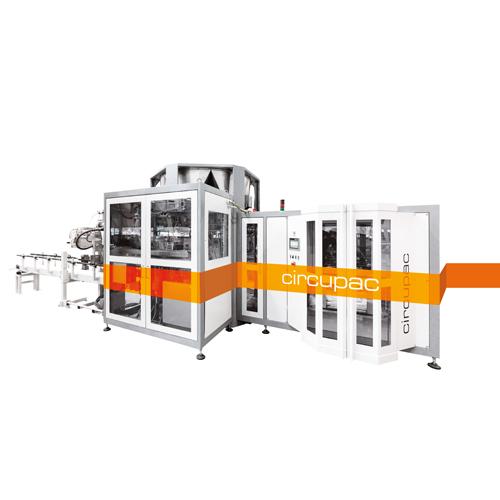
Open mouth bag filling machine for powders
The packaging of powdery products such as flour can be challenging as it is cru...
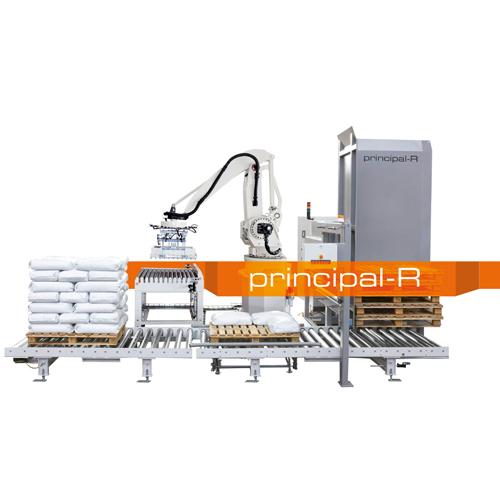
Robot palletizing system
If you are a relatively large-scale producer, packing and transporting large quantities of products ...

High containment split butterfly valve
Powder containment is the cornerstone of chemical and pharmaceutical manufacturing. ...